When manufacturing compression coil springs (pressure springs), the tip part may be ground by "end face grinding", and this page will explain "spring grinding".
The difference between "grinding" and "polishing" In addition to manufacturing springs, the terms "grinding" and "polishing" are often used when working with metals. Grinding involves using a grinding tool, such as a grinding wheel or a superabrasive wheel, to scrape off the surface of the workpiece slightly with many cutting edges on the working surface of the grinding wheel, and to obtain the required dimensions, shape and surface roughness. It is a finishing method. Polishing, on the other hand, is a method of pressing loose or fixed abrasive grains against a workpiece at a constant pressure to smooth the surface.
Edge Grinding of Springs "Grinding the edges" refers to grinding the tip of a compression coil spring (end winding, etc.). The main purposes of spring end face grinding are as follows.
1. Prevent eccentricity and buckling of the load by improving the perpendicularity.
2.Reduced contact dimension
3.Prevents damage to mating parts when aligning the spring with other parts.
Basically, thin wire springs (wire diameter of 1 mm or less, spring index of 10 or more) are said to have no problem in terms of accuracy even if they are not ground. For example, compression springs with a wire diameter of 0.5 mm or less are often used without grinding because they prevent shape changes when ground, or have little effect on mating parts when using springs. is. However, in recent years, there have been many cases where end face grinding is required even for springs with thin wire diameters such as those mentioned above.
Grinding machine (end grinder) When grinding springs, it is common to use an end grinder, but depending on the number and shape of the springs, there are cases where the grinding is done manually with a double-ended grinder.
Types of Grinding Machines (End Grinders) Grinding machines are divided into "vertical end grinders" and "horizontal end grinders" according to the mounting direction of the grinding wheel (posture when the spring is ground) .
Grinding machine example
vertical end grinder |
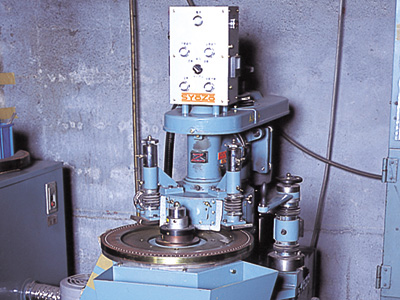 |
horizontal end grinder |
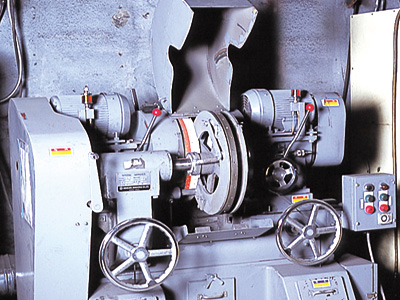 |
Both of the above end grinders have their own characteristics. The vertical end grinder has a horizontal work table for transporting the springs, and the weight of the springs can be used to insert and remove the springs, so manual work is easy. mentioned. In addition, it is also possible to automate the insertion of the vertical type. However, if it is set so that it can grind a spring with a high free height, the overall height of the machine will increase and there is a risk of vibration, so this end grinder is used for springs with a relatively short free height.
On the other hand, the horizontal end grinder cannot be automated and cannot use its own weight for inserting and ejecting the spring, so some auxiliary equipment is installed for grinding.
Grinding Types (Dry Grinding and Wet Grinding)
Spring grinding is mainly divided into "dry grinding" and "wet grinding".
Dry grinding is generally used for grinding coil springs in terms of workability, economy, and machine maintenance. Magnesia grinding wheels, which have a low coefficient of friction and are effective in preventing grinding burns, are widely used. Its use is said to be increasing, mainly for springs. In dry grinding, a dust collector is essential, and the dust collector itself is said to be effective in cooling the grinding wheel.
Used for grinding coil springs with large wire diameters. Almost no grinding heat is generated, heavy grinding is possible, and grinding powder is not scattered, so it is considered to be advantageous in terms of work environment.
Industry Grinding machine
>Click here for examples of grinding springs. List of links (Japanese Page)
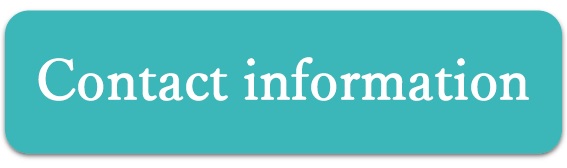
>Equipment introduction
>From order to delivery
>About special springs and custom-made springs
>Regarding small quantity and small lot production of springs
>Sales of spring materials
> About Spring Quotation
>Delivery of spring orders
>Fundamentals of spring design "Spring design procedure 7 points"
>Fundamentals of spring design "Five points for spring material selection"
>Fundamentals of spring design "Five points of compression spring design"
>Fundamentals of spring design "Five points of extension spring design"
>JIS standard for springs
>Customer's voice
>Frequently Asked Questions
>Quality Management Policy
|