日本の産業を支える ~顧客と一体になったばねづくり~ 大阪商業大学講演1
吉村篤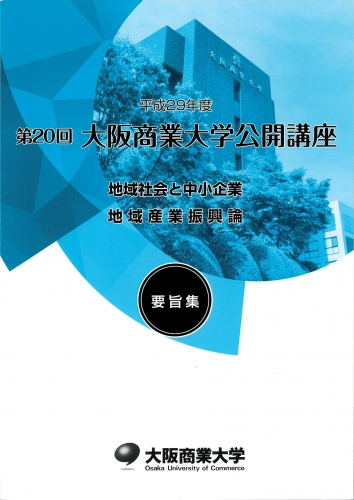
日本の産業を支える ~顧客一体となったばねづくり~
地域産業復興論
大阪商業大学講演記録1 2017年11月30日
フセハツ工業株式会社 代表取締役社長 吉村篤
会社概要
フセハツ工業株式会社の吉村篤と申します。弊社は、東大阪市の西堤本通りにあり、そこで70年ほどやっていて、創立は1950年、私で4代目になります。
戦後すぐに、1946年に祖父作田忠雄が「ばね作」を個人創業したのが始まりです。
1950年に「株式会社布施発条工業所」として法人化し、1966年に現在の社名「フセハツ工業株式会社」になりました。
従業員は、現在48名で、大体50人前後でやっている製造会社になります。
事業内容
事業の概要ですが、40%ぐらいは自動車関連のばねを作っています。
どこの部分を作っているかと言いますと、マニュアル車の中に入るクラッチリングを40%ほど生産しています。
今、どこにそんな車があるのかと思われるかもしれませんが、バスやトラックではまだかなり使われています。それから海外でも相当使われていいます。
生産量としては、リーマンショック前よりもやや増えているような感じです。
そして、ほかに作るところもないので、この分野ではうちが日本一です。逆に世界一を目指さないと生き残っていけないです。そこを目指していろいろ、工場改革をやっているところです。
そのほかに一般産業用ばねとして60%ぐらいです。
精密なものから日用雑貨的なものまで、さまざまなものを作っていますが、代表的なものですと、日本全国の美容院の椅子にはうちのばねがどこかに使われています。
最近では、耐熱ばね事業で、インコネルやハステロイといったニッケル合金の特殊なばねの試作サービスから量産まで行っています。
これらは、最近、ステンレス鋼線ですると錆やヘタリの恐れがあるので、より安全性やスペックの髙いインコネルでやりたいというお客さん、特に大手さんを中心に置き換えるところが増えてきていまして、
そういったサービスを、真空炉という特殊な熱処理ができるような炉も導入して展開しています。
そして、試作は1個からお受けするということで、「1個しかいらない」と言われたら、1個だけしか作らないというスタンスで、お客様のサービスに応えるようにしています。
しかし、1個から作ろうと思ったら、最新鋭のコンピューターの機械ばかりそろえても作ることができませんので、昔ながらの手巻き職人といいますか、そういったローテク技術を大切にしながら、ばねづくりを進めています。
それから、年配の方はご存じかと思いますが、エキスパンダーというスポーツ用ばね製品が昔ありましたが、うちの会社で製造していました。
実は、創業者である祖父が考え、作ったのがもともとの発祥です。実用新案を取っ手、昭和30年代、40年代に大量生産して、アメリカやオーストラリアなど、海外にもどんどん輸出していた時代があります。
途中からスポーツのミズノさんのOEMでしばらくやっていましたが、現在はスポーツ用ばね製品は作っていません。
これ、実は、少し弱点がありまして、ばねが折れたり、ばねを体に挟んだりして、安全面では少し問題があって、最後のほうはゴムロープに変えたりして作っていた時代もありました。
当時の在庫がまだ少しありますので、元祖オリジナルエキスパンダーとしてのレトロな商品価値を認めてくださる方には、特別にお分けしています。今では、どこにも売っていない希少な商品となりました。
また、弊社は、全国から修学旅行生を受け入れる事業にも協力していまして、うちのばね工場を見学していただいた後、いろんな昔あったスポーツばねなどを体験していただいています。
学校の先生にも非常に喜んでいただいて、お土産に皆さんに持って帰っていただいています。
今の若い子は、町工場など見たことがないので、東大阪モノづくり観光推進協会に所属して、少しでも若い子にそういう現場を見ていただきたいので、会社として取り組んでいます。
ばねの製造について
ばねの製造をほとんどの方はご覧になったことがないと思いますので、少しばねを作っているところを見ていただこうかなと思います。
ねじりばねと言われているばねがあります。
両側からアームが出てきまして、複雑な形状に曲げていく機械です。両端が360度回転する。中心も360度回転する。こんな機械で作っています。
これはRX-40という名前の機会ですが、たぶん、今、日本でなる中では一番いいと言われている機械です。
昔の職人さんの手加工も忠実に再現できるような、昔は突いて曲げるタイプが多かったのですが、最近は挟んで曲げると言いますか、傷が付かない人間的なタッチで曲げるようなフォーミングマシンが出てきてます。
これはまた、全然形状がちがう、ダルマ状のスプリングの製造例です。こういう形状のものも作れたりします。
これも同じフォーミングマシンですが、また少し違います。真ん中から出てきて、前後・左右・上下にいろいろな治具をはめるようになっていて、曲げるタイプのものです。
そして、最後はロボットアームで掴み取り出すのが自動化されています。
前に出てピッと触っているのはタッチ式のセンサーで、これによって、全数角度検査を行います。すべてデータがモニターに出て、自動選別されるような形になっています。
これはまたタイプの違う機械で、引張りばねを製造する機械です。両端にフックがついているタイプのばねです。
前のほうでフックを成形して、それが後ろにいってセカンドフォーマーという赤い部分の機械で後ろのフックを立ち上げるようになっています。
タッチしてすべてのフックの角度を自動的に検査します。駄目だったら、自動的に止まります。
9割までは機械が持っていってくれるのですが、やっぱり最後は人間の手で調整して、加工治具を溶接したり、削ったり、研磨して微調整をして仕上げます。
動いているところを見ると簡単にできそうに思うのですが、なかなかそういうわけではなくて、動くまでが結構微調整が大変です。
このあと、ばねは熱処理を行います。熱処理をすると、寸法が変化しますので、それを逆算して巻取りを行います。
フックも角度の形状がすべて変わってしまいますので、それも材料によってどう変わるかということが分からないです。
同じメーカーの同じ材料を仮に仕入れたとしても、やっぱりロットや作った時期によって微妙に変わります。
また、微妙にこのフックの角度を調節しないと駄目です。あと、温度を調節しないといけません。
ばねと言えば、一般にはこの圧縮コイルばねです。
下のくさび形の加工治具を差し込んで、ピッチを作るタイプのものです。
手前に円盤みたいに付いているのは、これは非タッチ式センサーになります。これで全てのばねの自由長を測定します。
そして、モニターに出て自動選別します。
太いばねについては、このあと研磨工程と言いまして、両端を削る作業が必要になっています。
どういうふうに削っているのかと言いますと、このばねの大きさに合わせた円盤とカラー(ブッシュ)を用いて、1個1個差し挟んで、両側から砥石を押していって削ります。
これは横型タイプの研磨機になります。
こういった削るための道具、ばねに合わせたパイプや円盤は、自社でほとんど作っています。
ばねを巻きだけではなくて、ばねを作るための道具も自社で作る技術がないと、お客さんの言うコストでものづくりはできません。
だから、ばねを巻く機械以外にも工作機械、旋盤、フライス盤、ボール盤など、工作機械を一式揃えています。
これは縦タイプの研磨機です。ばねの大きさに合わせて円盤に穴があけられています。
そこにばねをどんどん放り込んでいって、削れた状態で出てくるというものです。
ばねの研磨機ですが、これは今、日本で作っているところがどんどんなくなってきていまして、実質的には1社しかないような状況になっています。
これは小物ばねです。かなりのスピードで生産しています。これもすべて全数検査を行って位て、自動的に選別を行います。
最近の機械は、寸法が狂ってきたなと思ったらそれをまたデータからキャッチして、自分で修正して巻いたりもします。
最新のばねの機会というのは、大体こういう形で生産を行っています。